Aircrete Wall Tile Is A Collection Of Nesting Sculptural Tiles Cast For Eco-Friendly Building.
- Aircrete Africa
- Jan 27, 2018
- 4 min read
Updated: Feb 17, 2018
Natural building materials, the mix creates an aerated tile providing insulation, structure and fire protection in one lightweight product. The tiles is the perfect choice for both exterior (Fence, Pillars, Window frames) and Interior (rooms, offices, toilet), where durability is a priority. The tiles that easy to install and manage like standard tile.
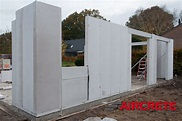
Autoclaved aerated concrete
"Aerated concrete" For cellular concrete (foamed concrete), see Types_of_concrete § Cellular_concrete. For lightweight blocks,
Aerated autoclaved concrete - close-up view

Autoclaved aerated concrete tiles of various shapes and sizes
On the right, green AAC blocks are being fed into an autoclave to be rapidly cured under heat and pressure
Autoclaved aerated concrete (AAC), also known as autoclaved cellular concrete (ACC), autoclaved lightweight concrete (ALC), autoclaved concrete, cellular concrete, porous concrete, Aircrete,
Hebel Block, and Ytong is a lightweight, precast, foam concretebuilding material invented in the mid-1920s that simultaneously provides structure, insulation, and fire- and mold-resistance. AAC products include blocks, wall panels, floor and roof panels, cladding (façade) panels and lintels.
History
AAC was perfected in the mid-1920s by the Swedish architect and inventor Dr. Johan Axel Eriksson,working with Professor Henrik Kreüger at the Royal Institute of Technology.
The process was patented in 1924. In 1929, production started in Sweden at the city of Yxhult. From "Yxhults Ånghärdade Gasbetong" later became the first registered building materials brand in the world: Ytong. Another brand “Siporex” was established in Sweden in 1939 and presently licenses and owns plants in 35 locations around the world. The second major international cellular concrete Hebel brand goes back to company founder and technicians Josef Hebel from Memmingen. In 1943, the first Hebel-plant was opened in Germany.
Originally Ytong autoclaved aerated concrete in Sweden was produced with alum shale, whose combustible carbon content was beneficial in the production process. Unfortunately, the slate deposits used for Ytong in Sweden also contain a very low level of natural uranium, which makes the material give off radioactive radon gas in the building. In 1972, the Swedish Radiation Safety Authority pointed out the unsuitability of a radon-emitting construction material, and the use of alum slate in the production of Ytong ceased in 1975.
By using new formulations, containing only quartz sand, calcined gypsum, lime (mineral), cement, water and aluminum powder, Ytong produced a new type of aerated concrete which no longer contains alum slate and thus has eliminated the problem of radon exposure from this raw material. The production of this white autoclaved aerated concrete is now state of the art and similar formulations are used by all producers around the world.
In 1978 The Swedish team of Siporex Sweden opened the Siporex Factory in Kingdom Saudi Arabia - the "Lightweight Construction Company - Siporex - LCC SIPOREX" which have supplied the Middle east and Africa and Japan by most of its need . The LCC SIPOREX FACTORY is operating for more than 40 years .
Today aerated concrete is produced by many companies, particularly in Europe and Asia. There is some production in the Americas, and in Africa there is one plant in Egypt.
AAC production in Europe has slowed down considerably, but the industry is growing rapidly in Asia due to strong demand in housing and commercial space.
China is now the largest Aircrete market in the world with several hundred factories. China, Central Asia, India, and the Middle-East are the biggest in terms of AAC manufacturing and consumption.
The product aircrete is sold, like other masonry materials, under many different brand names. Ytong and Hebel are brands of the international operating company Xella headquartered in Duisburg. Other more internationally renowned brand names in Europe are H + H Celcon (Denmark), or Solbet (Poland).
Uses
AAC is a highly thermally insulating concrete-based material used for both internal and external construction. Besides AAC's insulating capability, one of its advantages in construction is its quick and easy installation, because the material can be routed, sanded, or cut to size on site using standard carbon steel power tools.
AAC is well suited for urban areas with high rise buildings and those with high temperature variations. Due to its lower density, high rise buildings constructed using AAC require less steel and concrete for structural members. The requirement of mortar for laying of AAC blocks is reduced due to the lower number of joints. Similarly, the material required for rendering is also lower due to the dimensional accuracy of AAC. The increased thermal efficiency of AAC makes it suitable for use in areas with extreme temperatures, as it eliminates the need for separate materials for construction and insulation, leading to faster construction and cost savings.
Even though regular cement mortar can be used, most of the buildings erected with AAC materials use thin bed mortar in thicknesses around ⅛ inch, depending on the national building codes. AAC materials can be coated with a stucco or plaster compound to guard against the elements, or covered with siding materials such as brick or vinyl. Every time you write a post, you can add it up to 3 different categories. Those categories will then appear in your blog’s navigation menu, so choose categories that you normally post about and also serve as the main topics of your blog, e.g., Food, Fashion, Travel, etc.
Comments